It seems like you’re looking for information about both aluminum CNC milling parts and casting processes involving CNC. Let’s break down each aspect:
Aluminum CNC Milling Parts:
Process Overview:
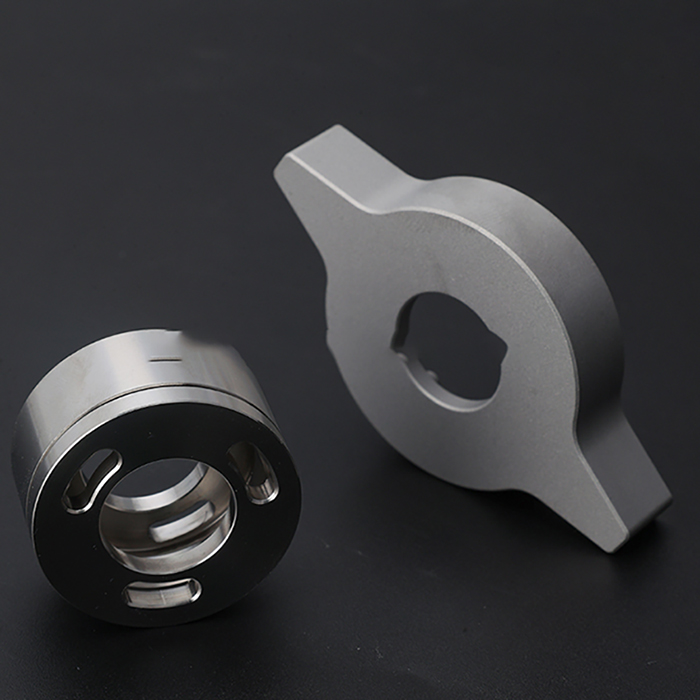
1.Material: Aluminum is a widely used material in CNC milling due to its lightweight, strength, and corrosion resistance.
2.CNC Milling: This process involves using CNC machines (computer-controlled mills) to remove material from a solid block of aluminum to create the desired shape and features.
3.Applications: CNC milling is used to manufacture a wide range of aluminum parts, including components for aerospace, automotive, electronics, and consumer goods industries.
4.Advantages: Precision machining allows for tight tolerances, complex geometries, and high-quality surface finishes.
Casting with CNC Machining:
Process Overview:
5.Casting: In aluminum casting, molten aluminum is poured into a mold cavity where it solidifies to form the desired shape.
6.CNC Machining After Casting: Once the aluminum part is cast and solidified, CNC machining can be used for several purposes:
7.Finishing: CNC machining is used to remove excess material, smooth surfaces, and achieve precise dimensions.
8.Drilling and Tapping: CNC machines can add holes and threads as required.
9.Surface Treatments: CNC can be used to apply surface treatments like polishing or anodizing.
10.Applications: Casting followed by CNC machining is suitable for producing parts with complex shapes, large volumes, or where design changes are likely during the production process.
11.Advantages: Cost-effective for large production runs, flexibility in design, and can achieve excellent surface finishes and dimensional accuracy.
Choosing Between CNC Milling and Casting with CNC:
Considerations:
12.Complexity and Design: CNC milling is ideal for intricate designs and precise dimensions directly from solid aluminum blocks. Casting with CNC machining suits complex shapes that are impractical or costly to machine entirely from solid.
13.Cost and Volume: CNC milling from solid stock is suitable for smaller production runs or prototypes. Casting followed by CNC machining is more cost-effective for larger volumes due to reduced material waste.
14.Material Properties: CNC milling preserves the inherent strength of aluminum, while casting can introduce slight variations in material properties depending on the casting method used.
Conclusion:
Both CNC milling of aluminum parts and casting with subsequent CNC machining are valuable processes in manufacturing, each with its strengths depending on the specific requirements of your parts. Understanding your project’s needs in terms of complexity, volume, budget, and material properties will help determine the most suitable manufacturing method.
If you have specific questions or need further details on any aspect, feel free to ask!