Rapid Tooling Services
Rapid tooling making is a fast, convenient and cost-effective technology, which is characterized by a short molding cycle, simple process, easy promotion, low molding cost, accuracy, and longer tooling life that can meet functional needs. It is especially suitable for the development and trial production of new products, process verification, and functional verification, as well as multi-variety and low-volume production. With our rich knowledge and customized manufacturing experience, we can help you accelerate the product to market.
What is Rapid Tooling
Most traditional manufacturing process requires custom tooling to create end-use parts. However, tooling comes with high upfront costs and weeks or month-long lead times from services providers. Rapid tooling is more and more popular in these years, which greatly reduces the time needed for mold-forming process and therefore increases the speed of production. This in turn reduces the time to market allowing companies to increase profits. Rapid tooling also allows the ease of product customization due to its flexibility in tool design, ability to adapt to customers’ specifications, and most importantly, does not require high volume to break even. Conceptual designs can be further improved without incurring high costs compared to conventional manufacturing processes. These factors in Rapid tooling attribute to high performance manufacturing and high quality products.
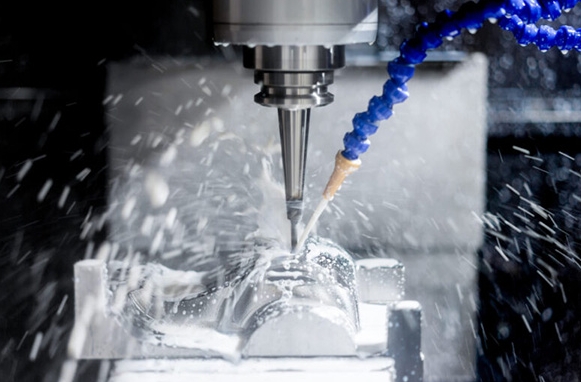
Rapid Tooling Materials
Steel Mold Tooling
In HAOSTAMPING, we only utilize the superior quality material for rapid tooling. E.g. the steel P20. When refers to steel, it is widely known for its unique characteristics, and is a popular and widely used material. Steel is a solid, sturdy and high-quality tooling material, which can also be used to produce wear-resistant and corrosion resistant engineering grade plastic molds. The main reason for using this tooling material is that it contributes to a better glossy surface finish.
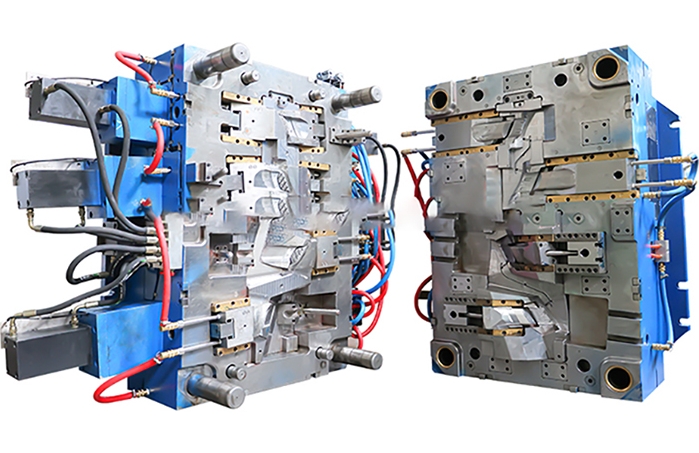
Types of Rapid Tooling
Direct Rapid Tooling
- Create a 3D CAD model of a mold or tool.
- Send the file to a machine to make the actual mold or tool that will be used for producing prototypes.
- The tool or mold produced can then be used directly to make prototypes—typically a very small number of them.
Indirect Rapid Tooling
- Create a 3D CAD model of the master mold or tool.
- Send the file to a machine to create a master mold or tool, also known as a pattern. This master pattern is typically very durable.
- Make more molds or tools based on the master pattern. The new molds or tools can be made from different types of materials with different properties.
A single master pattern can produce many different tools or molds in large or small quantities, which in turn can produce many more prototypes.
Direct Rapid Tooling | Indirect Rapid Tooling | |
Pros | · Faster production and shortened lead times · Can produce multiple prototypes from a single mold or tool ·Allowing to make multiple molds quickly as your design changes | · The master pattern is very durable and rarely gets damaged during the prototyping process · Can make either hard or soft tools based on customer’s needs. Hard tools are ideal for complex designs,while soft tools can be used for simple designs or cost-effective prototype testing. · Ideal for experimenting with different materials |
Cons | · May not be appropriate for highly complex designs or materials that require a durable mold or tool to produce intricate details · Could result in higher product development costs if create multiple moldsfor each new design iteration | · Longer production time and Higher cost · Not always a good option if the design will change significantly during the prototyping stage · May require higher quality materials to make a robust master pattern |
Benefits of Rapid Tooling

Fast Delivery
In HAOSTAMPING, there are hundreds of shared mold base and a number of precision machines which allow us making your rapid parts in a short time. Most significantly, we can ship to anywhere in this world.
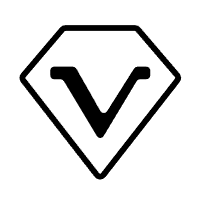
Best Quality and Competitive Price
HAOSTAMPING has acquired an extensive tooling capability and is supported by a team of people who have skills and technical knowledge you can rely on. We can find the best way for your project to save the cost and keep high-quality parts. Generally, we use the shared mold base system so the tooling cost can be 30-50% lower than that of tradition production tooling.

Multiple material options
The rapid tooling process provides a wide range of material options as any material available for injection molding can be formed by the rapid tooling process. If customers unsure exactly which material is more suitable, then our engineers will help clients to choose the right material according to the requirement of part.
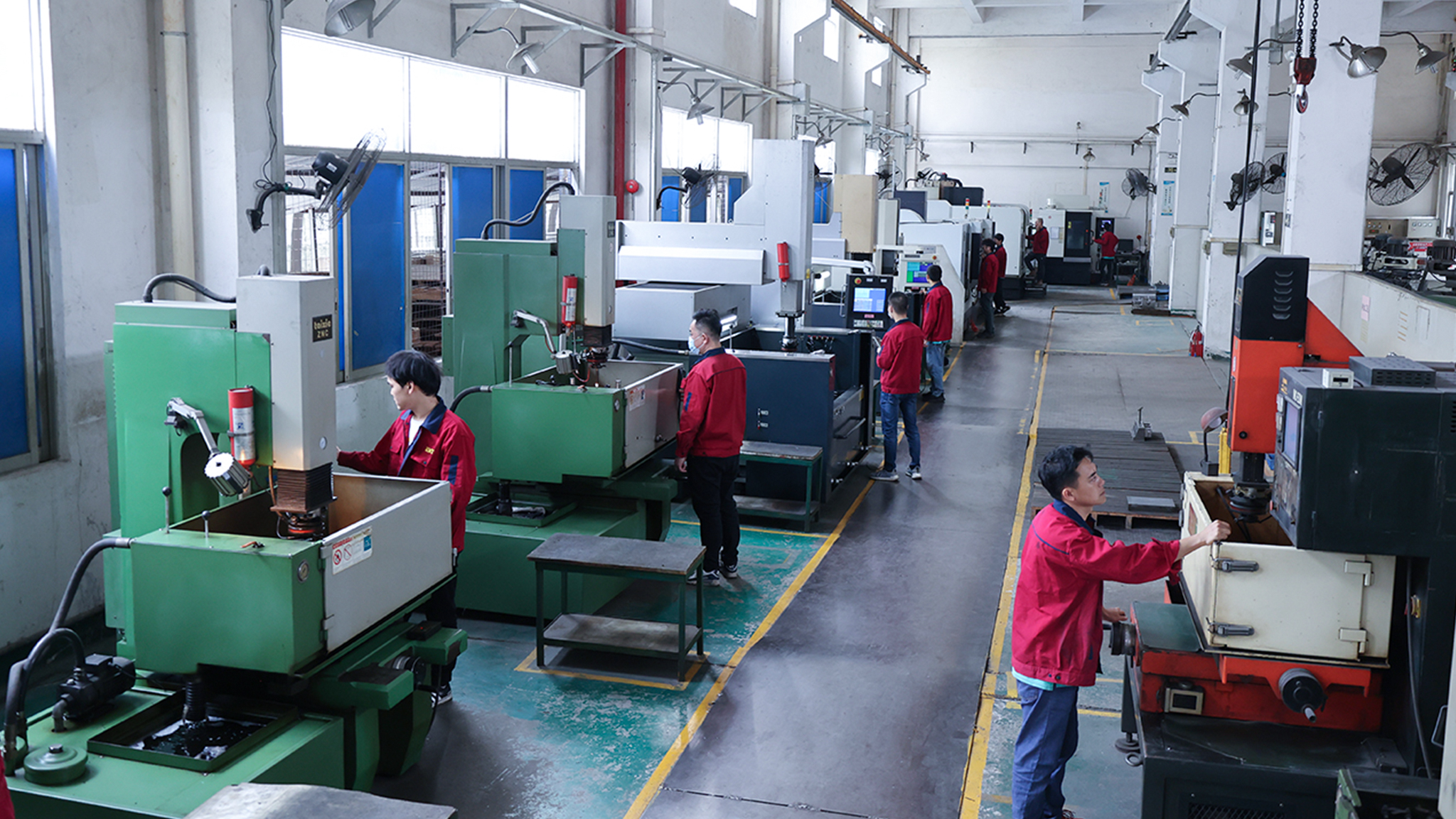
How Make Rapid Tooling in HAOSTAMPING
- DfM provided within 24h after customer confirms the order.
- Tooling design and cutting main steel at the same time after DFM approval.
- CNC machining cavity and core inserts; matched MUD will be checked out and send to tooling assembly workshop.
- Auxiliary tooling components machined out and send to tooling assembly workshop.
- Tooling fitting and polishing.
- Tooling inspected by master and send to injection molding workshop to test.
- Initial samples after engineers checked and send to .dimensions inspect.
Rapid Tooling FAQs
Cases of Rapid Tooling Making
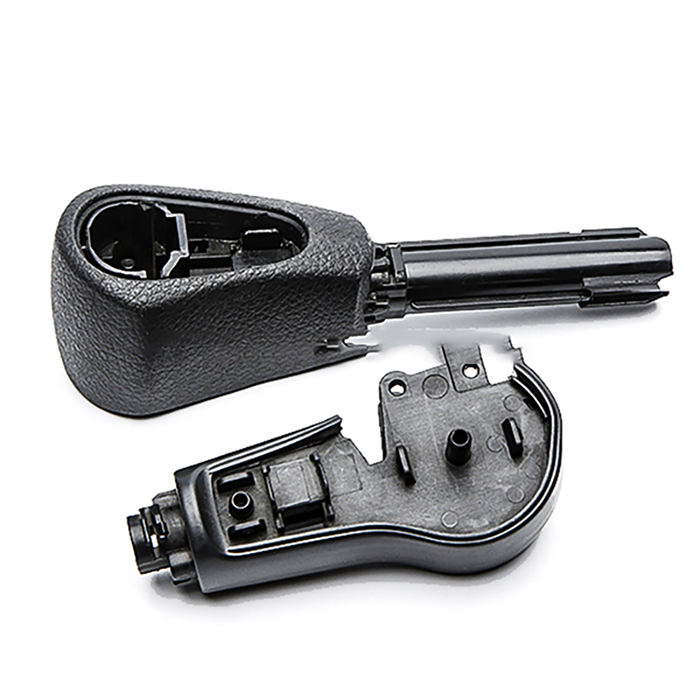
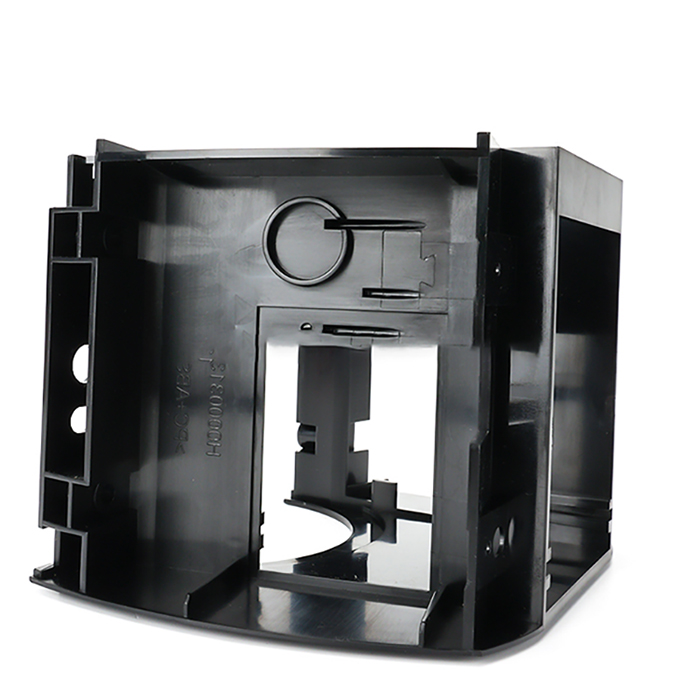
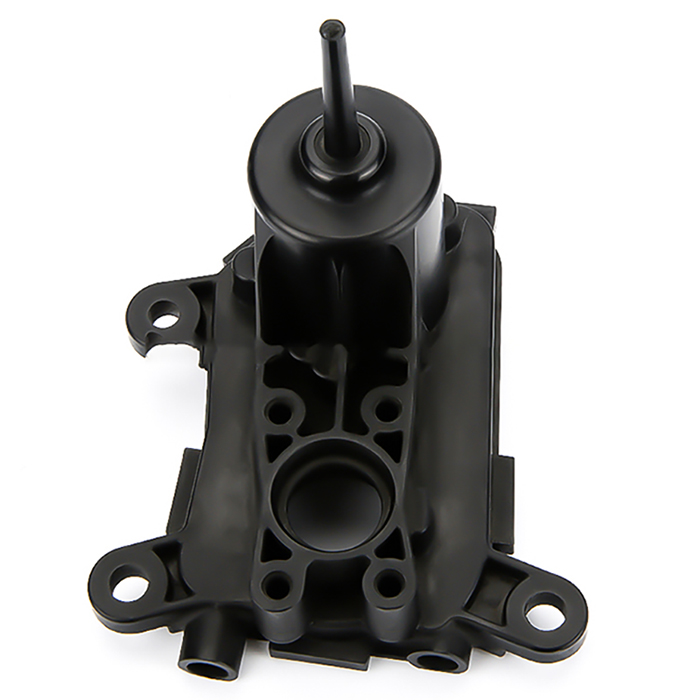
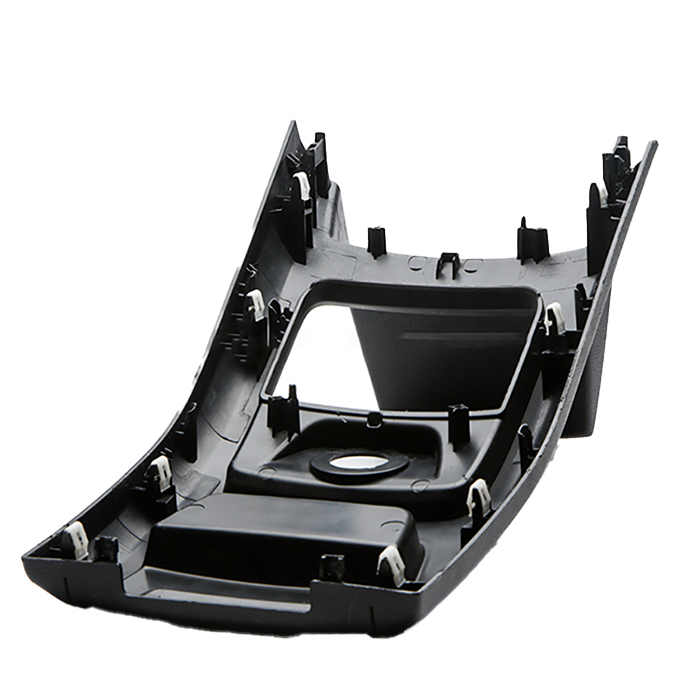
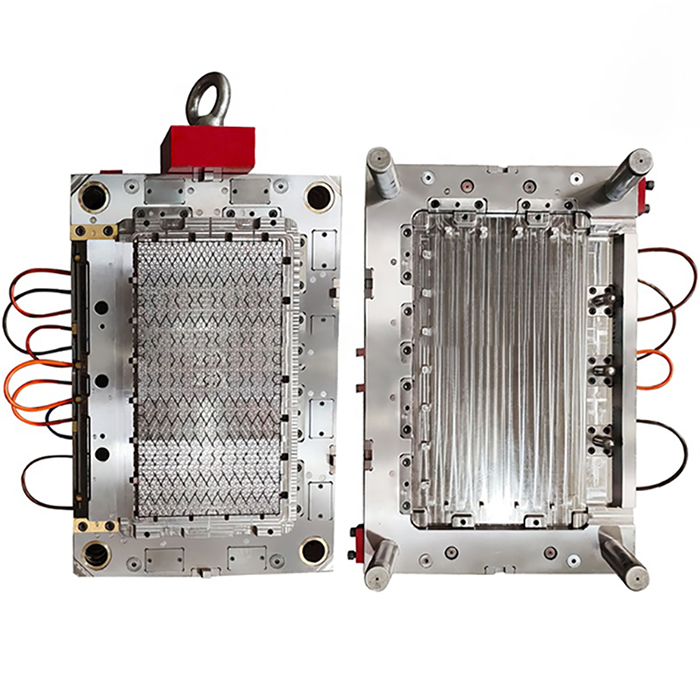
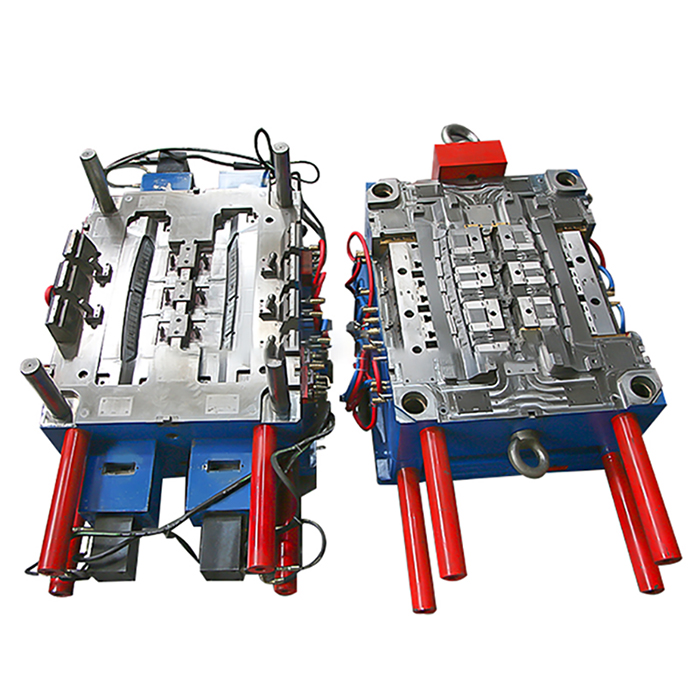
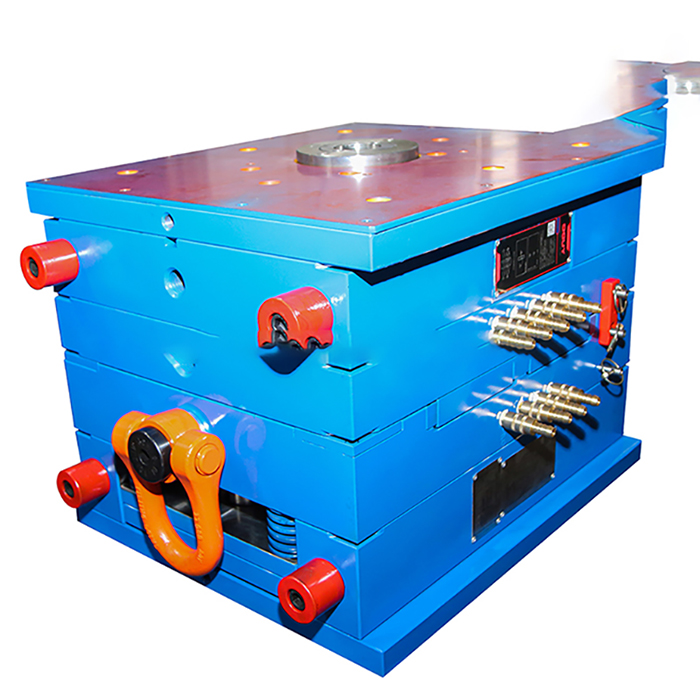
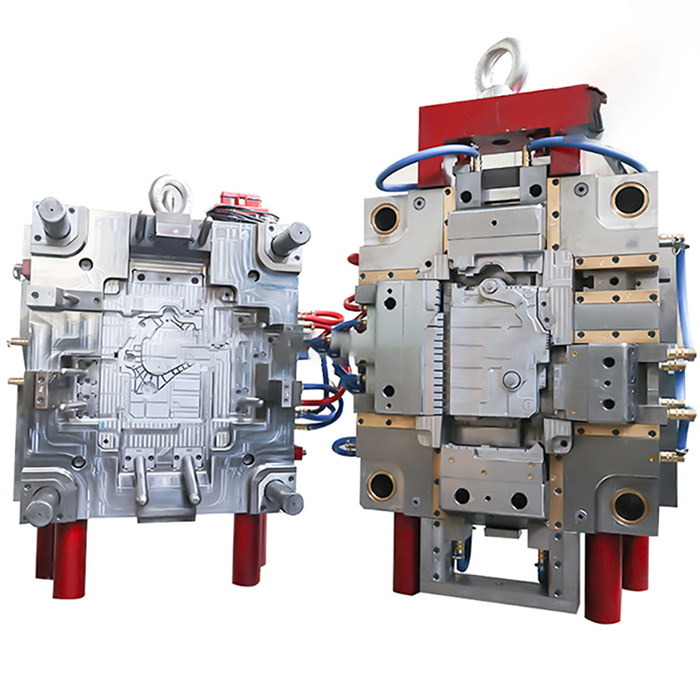
Ready to Work On your Next Project?
Let us help you provide high quality parts in short time. Get your project started now!