Certainly! CNC machining is a versatile method for producing precision metal parts, and finding cost-effective solutions often involves considering a few key factors:
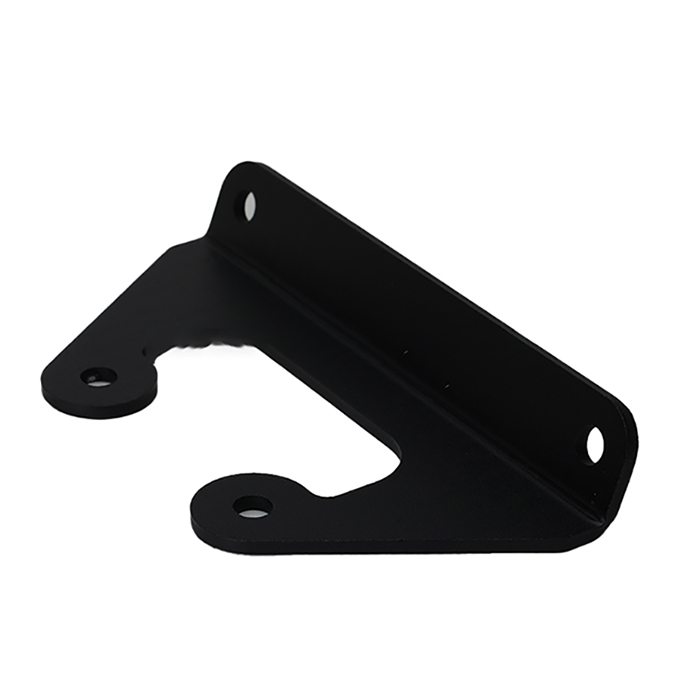
1.Material Selection: Choose the right material for your parts. Common metals like aluminum and stainless steel are cost-effective and widely used in CNC machining due to their machinability and durability.
2.Design Optimization: Simplify your design to minimize machining time and material waste. Complex designs with intricate features can increase machining costs significantly.
3.Batch Size: Larger production runs typically reduce per-part costs due to economies of scale. If feasible, consider batch ordering to lower unit costs.
4.Tolerance Requirements: Specify tight tolerances only where necessary. Looser tolerances can reduce machining time and cost.
5.Supplier Selection: Research and compare quotes from different CNC machining suppliers. Look for reputable companies that offer competitive pricing without compromising quality.
Regarding CNC lathes specifically, they excel at cylindrical parts and can be cost-effective for turning operations. Here are some tips for optimizing costs when using CNC lathes:
6.Material Utilization: Minimize material waste by optimizing stock sizes and using efficient cutting strategies.
7.Tooling Efficiency: Proper selection and maintenance of cutting tools can enhance machining efficiency and reduce overall costs.
8.Setup Time: Reduce setup time by standardizing setups or using quick-change tooling systems.
9.Programming: Efficient CNC programming can optimize tool paths and reduce machining time.
By considering these factors and working closely with a reliable CNC machining provider, you can achieve cost-effective production of metal parts using CNC lathes. If you need more specific guidance or have further questions, feel free to ask!