It seems like you’re interested in the combination of casting and CNC machining specifically related to mineral casting. Let’s delve into what this involves:
Mineral Casting:
Mineral casting, also known as polymer concrete, is a material made from mineral fillers (such as quartz gravel or granite aggregates) bonded together by a polymer resin. This composite material offers several advantages over traditional materials like cast iron or steel, such as high stability, vibration dampening properties, and excellent thermal stability.
Casting Process:
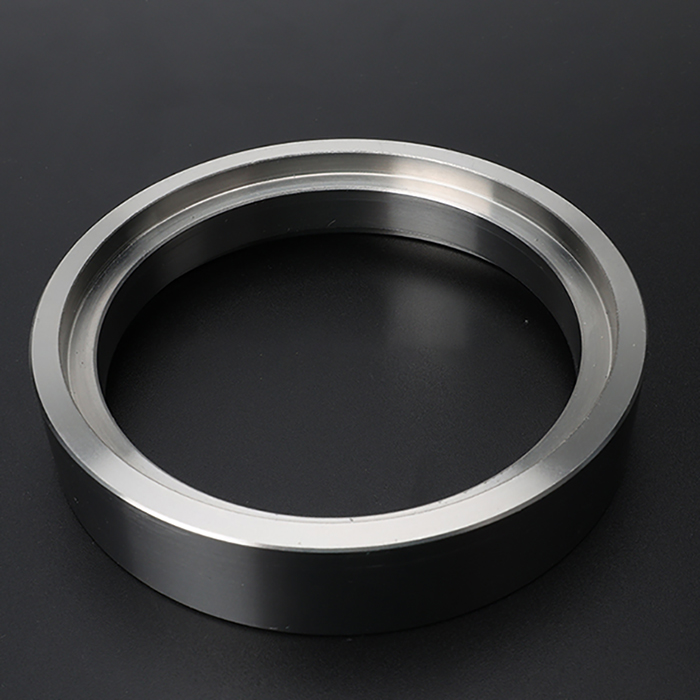
1.Mold Creation: The mineral casting process begins with creating a mold or form into which the mineral mixture will be poured. This mold defines the shape and dimensions of the final part.
2.Material Mixing: Quartz gravel or granite aggregates are mixed with a polymer resin binder. This mixture is then poured into the prepared mold.
3.Curing: The filled mold undergoes a curing process where the resin polymerizes and hardens, bonding the mineral particles together into a solid composite.
4.Demolding: Once cured, the mineral casting is removed from the mold. At this stage, the casting typically requires some machining to achieve precise dimensions and surface finishes.
CNC Machining on Mineral Casting:
After the mineral casting has been demolded, CNC machining can be applied to refine the part:
5.Precision Machining: CNC machines are used to remove excess material, achieve tight tolerances, and create the necessary features (holes, threads, surfaces).
6.Surface Finishing: CNC machining can improve the surface quality of mineral castings, ensuring they meet required specifications for smoothness and texture.
7.Complex Geometries: Mineral casting can be CNC machined to create complex shapes that would be difficult or impossible to achieve with traditional casting methods alone.
Advantages of Mineral Casting with CNC Machining:
8.High Stability: Mineral casting offers excellent dimensional stability and resistance to temperature fluctuations, making it suitable for applications where precision and reliability are critical.
9.Vibration Dampening: The composite material’s inherent properties dampen vibrations, making it ideal for machinery and equipment where smooth operation is essential.
10.Cost-Effectiveness: Combining casting with CNC machining can reduce overall production costs compared to machining from solid metal blocks, especially for larger and more complex parts.
Applications:
Mineral casting with CNC machining finds applications in various industries:
11.Machine Tools: Components requiring high precision and stability, such as machine beds and slides.
12.Measurement Equipment: Coordinate measuring machines (CMMs) and other precision instruments benefit from the stability and vibration dampening properties of mineral casting.
13.Medical Devices: Equipment requiring hygiene, precision, and durability.
In summary, mineral casting combined with CNC machining offers a versatile solution for manufacturing components that demand high precision, stability, and cost-efficiency. If you have specific questions about applications or processes related to mineral casting and CNC machining, feel free to ask!