Sure! When it comes to manufacturing plastic parts like car mount holders through insert molding, the process involves a few specialized techniques that are well-suited for this application.
Insert Molding Process for Car Mount Holders:
1.Insert Placement: Insert molding involves placing pre-formed metal or plastic inserts (such as screws, studs, or metal parts) into the mold cavity before injecting the plastic resin. These inserts serve specific functions like providing attachment points or reinforcement within the part.
2.Mold Design: The mold for insert molding is designed to accommodate the inserts securely in place. This ensures that when the plastic resin is injected, it flows around the inserts to form a strong bond.
3.Injection Molding Process:
4.Insert Placement: Inserts are placed into the mold cavity manually or using automated systems.
5.Melt and Inject: Plastic resin pellets are heated and melted in the injection molding machine’s barrel. The molten plastic is then injected into the mold cavity under high pressure.
6.Encapsulation: The molten plastic surrounds and encapsulates the inserts, forming a single integrated part.
7.Cooling and Solidification: After injection, the mold is cooled to solidify the plastic resin around the inserts. Cooling time is critical to ensure the part solidifies properly without warping or defects.
8.Ejection: Once cooled, the mold opens, and the finished part is ejected. Ejector pins or mechanisms are used to remove the part from the mold.
9.Finishing: Post-processing steps may include trimming excess material, removing sprues (the channels through which plastic enters the mold), and any necessary surface finishing.
Benefits of Insert Molding for Car Mount Holders:
10.Strength and Durability: Inserts provide additional strength and rigidity to the plastic part, crucial for applications like car mount holders that need to support weight and endure vibrations.
11.Reduced Assembly Time: By integrating multiple components into a single molded part, insert molding reduces the need for secondary assembly operations, saving time and labor costs.
12.Design Flexibility: Insert molding allows for complex part geometries and integrates multiple materials into a single part, expanding design possibilities.
Applications of Insert Molded Car Mount Holders:
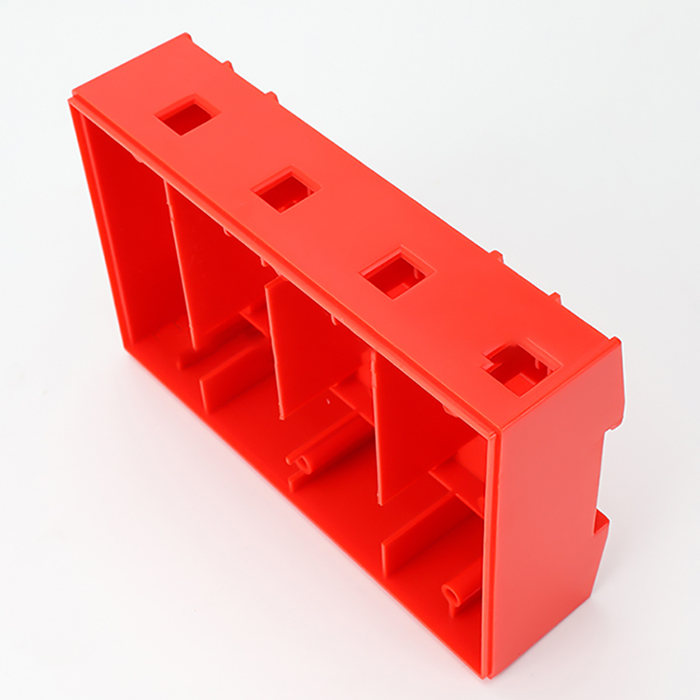
13.Secure Mounting: Inserts can be used to securely attach components like suction cups, hinges, or magnetic plates to the car mount holder.
14.Enhanced Functionality: Inserts can incorporate metal threads for screw attachment points or reinforcement for structural integrity.
Considerations:
15.Material Selection: Choosing the right plastic resin is crucial for achieving the desired mechanical properties such as impact resistance, heat resistance, and flexibility.
16.Insert Compatibility: Ensuring the inserts are compatible with the molding process and materials used is essential for achieving a strong bond and reliable performance.
In summary, insert molding is an effective process for manufacturing car mount holders, allowing for the integration of inserts to enhance functionality and durability. If you have specific questions about material choices, design considerations, or production feasibility for car mount holders, feel free to ask for more details!